Odchylenie wyniku rzeczywistego od zabudżetowanego dla obszaru produkcyjnego należy w pierwszym etapie podzielić na czynniki zależne i niezależne od działań osób odpowiedzialnych. Następnie podział ten powinien się sprowadzać do wydzielenia bardziej szczegółowych kategorii odchyleń, aby dokonać prawidłowej oceny efektywności zarządzania zakładem produkcyjnym. Dzięki temu możliwe będzie połączenie postawionych w budżecie celów z rzetelną oceną osiągniętych wyników oraz z systemem motywacyjnym.

Standardowe koszty wytworzenia odzwierciedlają stabilny poziom normatywnych kosztów generowanych przez obszar produkcji w dłuższym okresie, odpowiadających normalnemu wykorzystaniu zdolności produkcyjnych. Wysokość kosztów jest zależna od technicznych i organizacyjnych aspektów, aktualnych w momencie sporządzania kalkulacji.
Normalny poziom wykorzystania zdolności produkcyjnych na potrzeby kalkulacji nie jest ustalany na wolumen produkcji w jednostkach naturalnych (kg, m.b., szt.), lecz na roboczogodziny maszyn zamontowanych na liniach produkcyjnych. Każde przedsiębiorstwo musi samo określić zapotrzebowanie na wyroby gotowe w średniej perspektywie czasowej w celu wyeliminowania jednorazowych wahań koniunkturalnych bądź okoliczności leżących po stronie zakładu.
Czas ten uwzględnia system pracy zakładu (jedno- lub dwuzmianowy, ruch ciągły itd.), zatrzymania produkcji związane ze świętami, z planowanymi serwisami i remontami, ograniczenia produkcji spowodowane sezonem urlopowym lub sezonowością produkcji.
Liczba pracowników – zarówno bezpośrednio produkcyjnych, jak i w wydziałach pomocniczych – również powinna zostać dopasowana do normatywnych czasów czynności opisanych w kartach technologicznych wyrobów oraz do wielkości odpowiadającej normalnemu wykorzystaniu mocy wytwórczych.
Przykład analizy odchyleń
W przedstawionym w dalszej części artykułu przykładzie zaprezentowano standardowy (normatywny) rachunek kosztów pełnych odpowiadający normalnemu wykorzystaniu zdolności produkcyjnych. Oznacza to, że w przedsiębiorstwie zostały ustalone normy zużycia, wydajności i kosztów dla poszczególnych procesów produkcyjnych, które są na bieżąco analizowane i przeciwstawiane kosztom rzeczywistym.
Całość kosztów ponoszonych przez zakład produkcyjny w celu wytworzenia określonego wolumenu produkcji podzielono – na potrzeby skalkulowania jednostkowych kosztów wyprodukowania wyrobów gotowych – na następujące elementy kalkulacyjne:
- koszty materiałów bezpośrednich (surowce, mieszanki surowców, opakowania ochronne),
- stawki godzinowe maszyn produkcyjnych (działalność podstawowa),
- stawki godzinowe pracowników bezpośrednio produkcyjnych (działalność podstawowa),
- narzut kalkulacyjny obejmujący: koszty wydziałów pomocniczych nierozliczonych na wydziały podstawowe, koszty składowania materiałów oraz koszty mielenia odpadów produkcyjnych do powtórnego wykorzystania.
Najważniejszą częścią składową kosztów wyprodukowania wyrobów gotowych w zakładzie produkcyjnym są najczęściej koszty materiałów bezpośrednich: surowce, mieszanki surowców, receptury, opakowania ochronne itd. Opierając się na normatywach ujętych w kartach technologicznych produktów, wyliczamy zapotrzebowanie na materiały bezpośrednie, park maszynowy oraz personel produkcyjny, co przedstawiono w tabeli 1 – kolumny „Normatyw wg karty technologicznej” oraz „Standard”).
Pozostałe 74% artykułu dostępne jest dla zalogowanych użytkowników serwisu.
Jeśli posiadasz aktywną prenumeratę przejdź do LOGOWANIA. Jeśli nie jesteś jeszcze naszym Czytelnikiem wybierz najkorzystniejszy WARIANT PRENUMERATY.
Zaloguj Zamów prenumeratę Kup dostęp do artykułuMożesz zobaczyć ten artykuł, jak i wiele innych w naszym portalu Controlling 24. Wystarczy, że klikniesz tutaj.
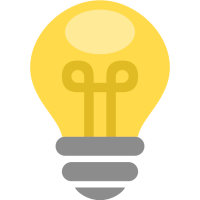
Pobierz pliki: